Copper etching slowly replaced woodblock printing when it became evident the detail that could be achieved with metal etching as opposed to carving wood. While metal etching has been around since as early as 5000 BC, it’s accredited to Martin Schongauer in the 1430s for creating the technique known as intaglio. This is where grooves in metal (copper, zinc, steel) created by scratching the surface with a tool called a burin or graver hold ink when it is poured over the plate. The plate is then wiped clean and ink only remains in the small grooves, when the paper is pressed against it, the ink transfers to the paper. Copper was originally preferred because it was easy to work with and didn’t rust but it has a cap use around 2000 or 3000 presses, steel replaced copper around 1822 because it would not flatten out during use but the lines had to be thicker. The invention of copper etching with acid meant even more detailed work. A copper plate can be coated in an acid-resistant wax, then drawn on with a fine needle, when the copper is dipped in acid, where the wax has been removed acid bites into the metal. This creates highly detailed prints. Since its invention artists have pushed it the technique to include different plates and etchings to be layered to get different values and ink colors. Different styles of this include Mezzotint by Ludwig van Siegen around 1642, Aquatint, Stipple, and Lithography invented by Alois Senefelder in 1798.
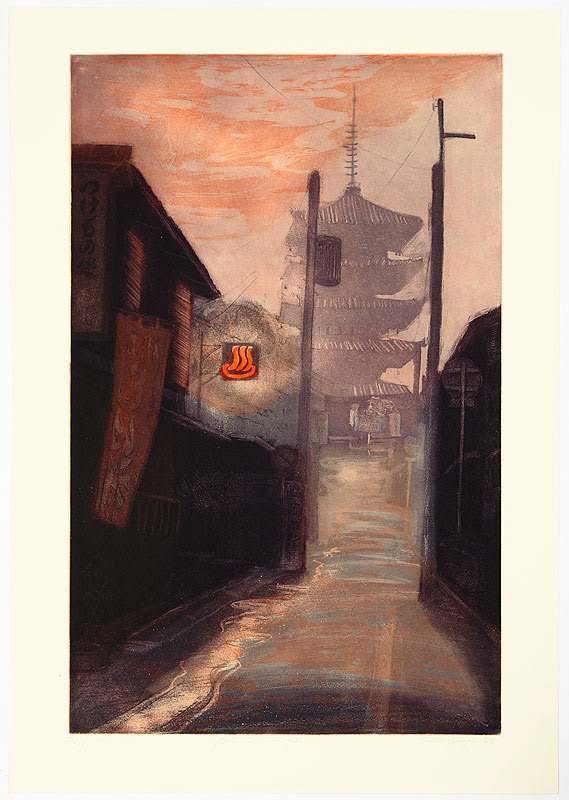
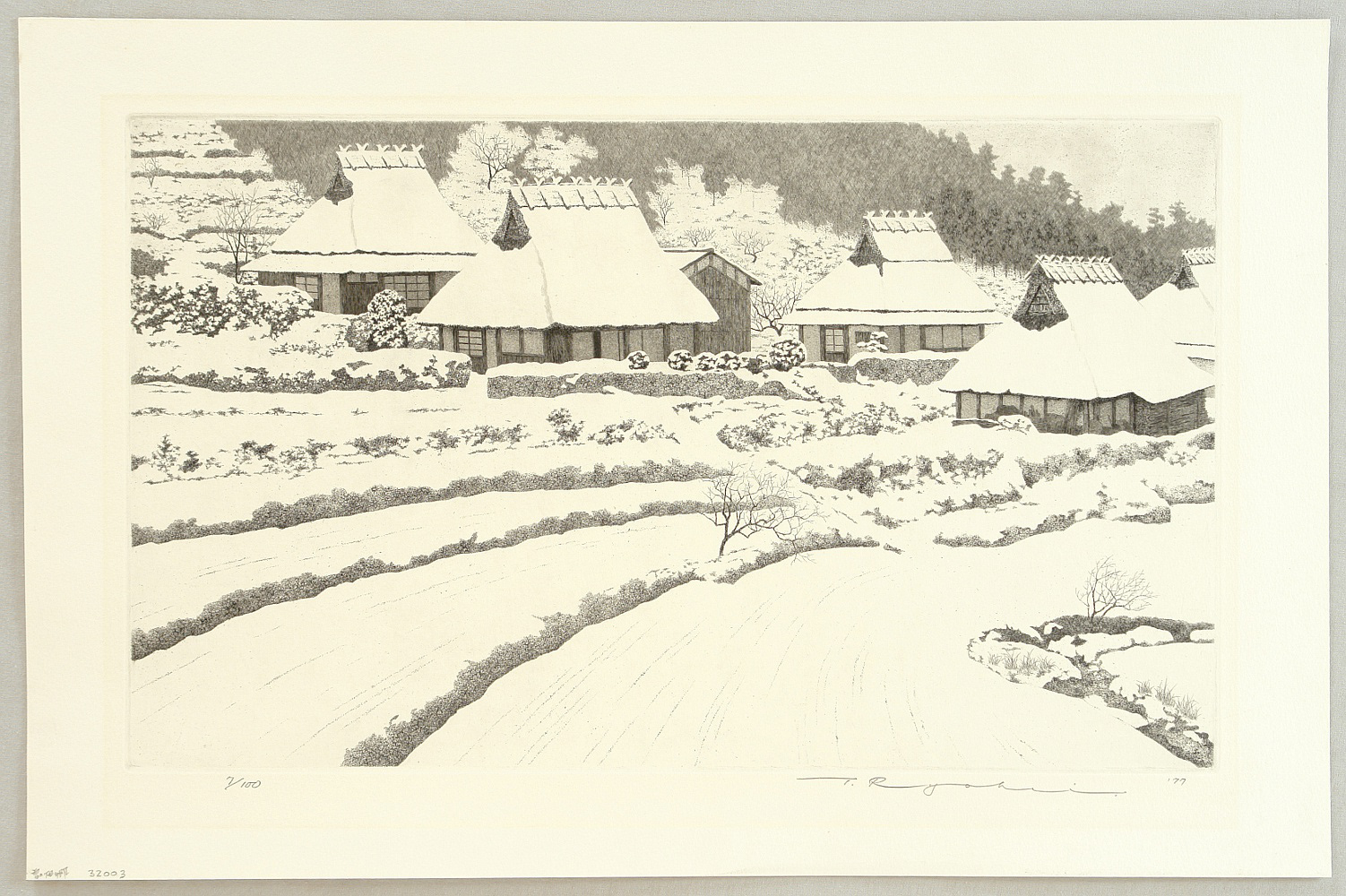
Not much has changed for copper etching and printing. While no longer necessary to print books, today hand etching copper is still popular in printmaking with the ability to achieve incredible color, detail, and texture it can create a look unachievable by a printer or digital renderings. It’s original use to create illustrations for books was very time consuming and limiting, now most books are mass produced and lack an illustrative design on every page. Today, printers use a laser to cut into metal plates making really precise cuts for a more predictable outcome. Thus instead of making all plates by hand and setting the type separately; designs can be drawn digitally or scanned and laser cut saving a lot of time for the carver. But the basic idea remains, with ink that settles in the grooves and transfers to paper. And while you can still hand press plates on a small scale, mass production mechanizes the press so large sheets of paper can run through the printer and be cut after for efficiency's sake. Other than artistically there is a practical use for analog: it is still used to make security paper like money, checks, and bonds, the idea is to include micro details that are unable to be reproduced without that plate. For added security, several different carvers will work on a single plate so there is no uniform style. In a digital age-old techniques still have a place, since copper plates are unable to be hacked, they're still the safest for printing currency. The ancient techniques have been refined but are still applicable to our art today, and can help us better understand how designs will be reproduced.
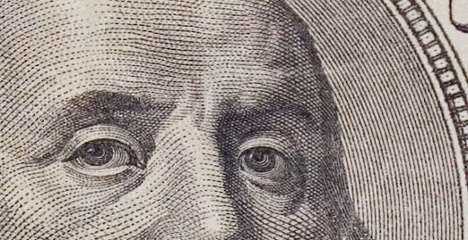
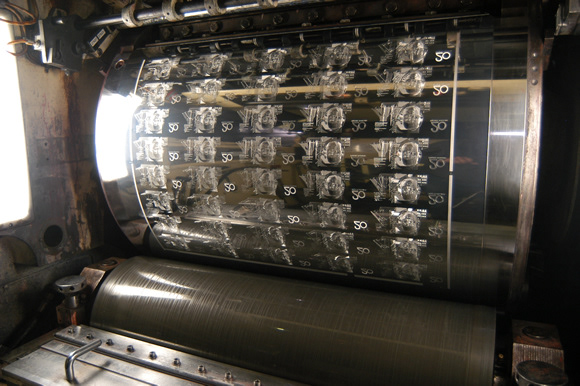
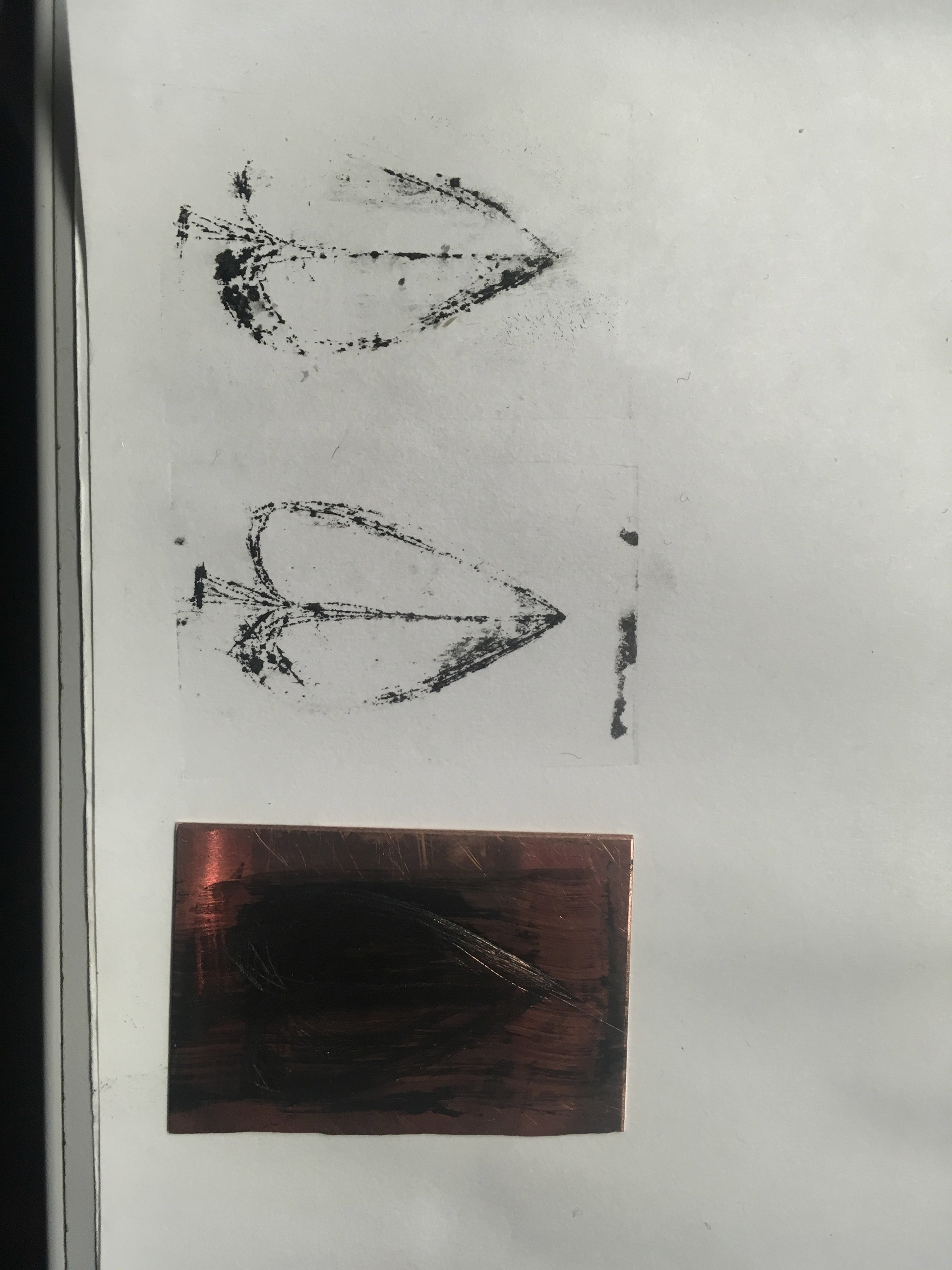
My attempt at copper etching, a scratched leaf.
Sources:
Ballou, Nancy. “Copper in the Arts.” Copper Development Association Inc., NACE International, Jan. 2012, www.copper.org/consumers/arts/2012/january/This_History_of_Inta.html.
Britannica, The Editors of Encyclopaedia. “Intaglio.” Encyclopædia Britannica, Encyclopædia Britannica, Inc., 29 Feb. 2012, www.britannica.com/topic/intaglio-printing.
“How Is a Book Printed?” Pan Macmillan, Pan Macmillan, www.panmacmillan.com/blogs/literary/how-is-a-book-printed.
Wanczura, Dieter. “Intaglio Printmaking.” Artelino, Artelino GmbH, 24 Dec. 2018, www.artelino.com/articles/intaglio_printmaking.asp.